Blog Post #2: Weeks 1-3, Getting Familiar with Materials & Expectations, by Henry Miller
- Henry Miller
- Jun 3, 2024
- 3 min read
Updated: Jun 17, 2024
Week One:
The upcoming 10 weeks present an exciting challenge as we dive into developing an Insulated Solar Electric Cooker (ISEC) for the Kindle Orphan Outreach in Malawi. Our team has been feverishly researching this unique facility, which provides care for vulnerable children and families in Malawi, while aiming to steward a nurturing, sustainable environment, which has been historically plundered for its natural resource rich landscape.
Through our professor, Dr. Pete Schwartz, as well as our advisors in Malawi, Salma and Viktor, we've learned about the daily challenges faced by communities in Malawi, including lack of access to reliable/renewable cooking fuel and the environmental toll of using firewood and charcoal. Following off the prototypes previously innovated by Dr. Schwartz, students Marilynn Vega, Alycia Darby, Cole Groom, and Henry Miller continued to redesign based on the challenges and resources available in Malawi.
Our preparation has included earning red-tag certification, which allows us to get hands-on experience in the wood and sheet metal shops right here on campus. We've been trained on using industrial machinery like drills and saws, while others like laser cutters, lathes and welding tools require more rigorous practice and additional certification.

Pictured Above: The RedTag Identification Card belonging to Henry, Third-Year Experience Industry Management (EIM) Student, after passing the required certification course
Beyond the technical challenges, we're exploring ways this certification could have a broader impact in our personal lives. Now we can fabricate gifts for loved ones back home or develop new skills marketable for fundraising issues we care deeply about.
Embarking on the ISEC Journey: Can We Deliver in 10 Weeks?
Our team has spent the last seven days researching and preparing for an ambitious 10-week challenge - developing an Insulated Solar Electric Cooker (ISEC) for the Kindle Orphan Outreach in Malawi. While earning our red-tag certification to use campus fabrication facilities, we've grappled with uncertainties around sourcing materials, overcoming technical obstacles, and adapting to Malawi's unique economic and cultural context. Transparently, we believe delivering a fully functional, field-tested ISEC prototype in this timeframe seems daunting, but we are up for the challenge.
Over the next 10 weeks, we'll pour our diverse skills and mindsets into overcoming the ISEC's challenges head-on. Undoubtedly there will be stumbles along the way, but each will provide invaluable lessons extending far beyond this specific device. We embrace this opportunity to create real impact through the ISEC design Pete has refined in an area that has a clear necessity and demand for the technology, making it appropriate for the course framework.
Week Two:
On our first day in the shop, we planned to test out different variations of concrete to figure out which would be the best insulator. Since we didn’t have any measuring devices available to us in the lab, we used an approximate concrete to water ratio of 3 to 1. The concrete mix consisted of sand, aggregate, and mortar. The mixture came out to be pretty coarse and more moist than we would prefer it to be. We made our sample pieces about half an inch thick as we had to take into consideration the total weight of the ISEC and the amount needed to insure proper insulation.
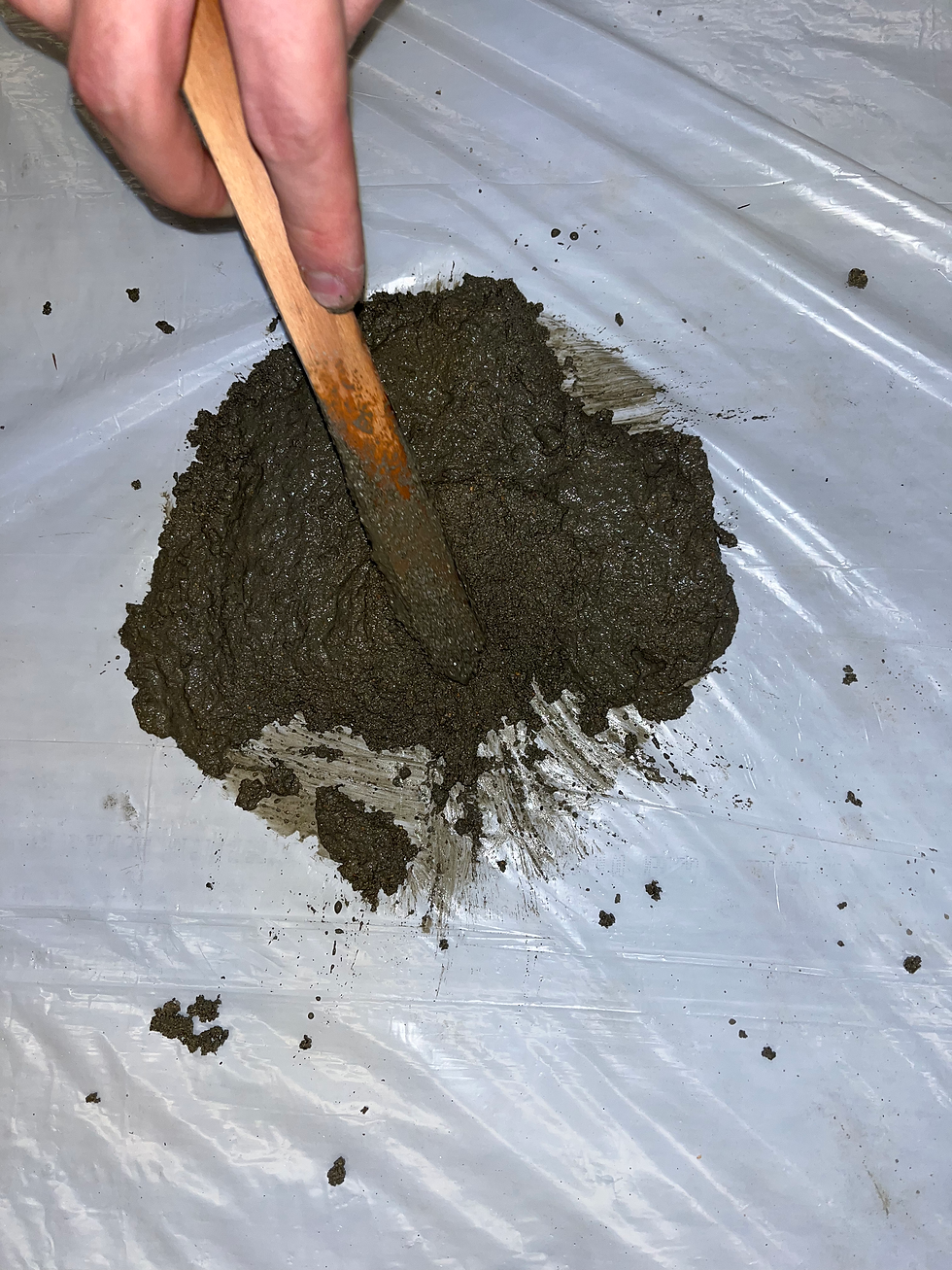
Pictured Above: Completed Mixture of Concrete with Fiberglass Insulation Mixed Throughout, No Chickenwire at this time
Our first sample was the control, which was unaltered. For our second sample, we applied a thin layer of fiberglass insulation on top of it to test thermal conductivity and insulation within the cooker. The third sample sandwiched a thin layer of fiberglass between ¼ inch layer of our concrete mixture. The last sample was a mixture of strands of fiberglass fabric and our concrete mixture.
After about a week of curing, our samples were ready. Although, they did not pass the cracking test. This can be attributed to an imprecise measurement of concrete and water.

Pictured Above: Adding Water to the Concrete Mixture to achieve desired consistency before packing Chickenwire
Week Three:
During Week Three, we primarily mixed concrete, further refining our measuring process. Only Alycia came into the proposed ISEC project with previous knowledge of material engineering, with experience in high-level Architectural Engineering classes at Cal Poly San Luis Obispo. The rest of the group contributed to individual research so as to maintain consistent understanding of the decisions we made, pertaining to heat retention from insulation and proper execution of concrete curation.

Pictured Above: Marilynn, Third-Year ENVM Student, safely testing various ratios of concrete material with an N95 Mask to protect from particle inhalation and gloves to protect from fiberglass irritation on their skin.
Comments